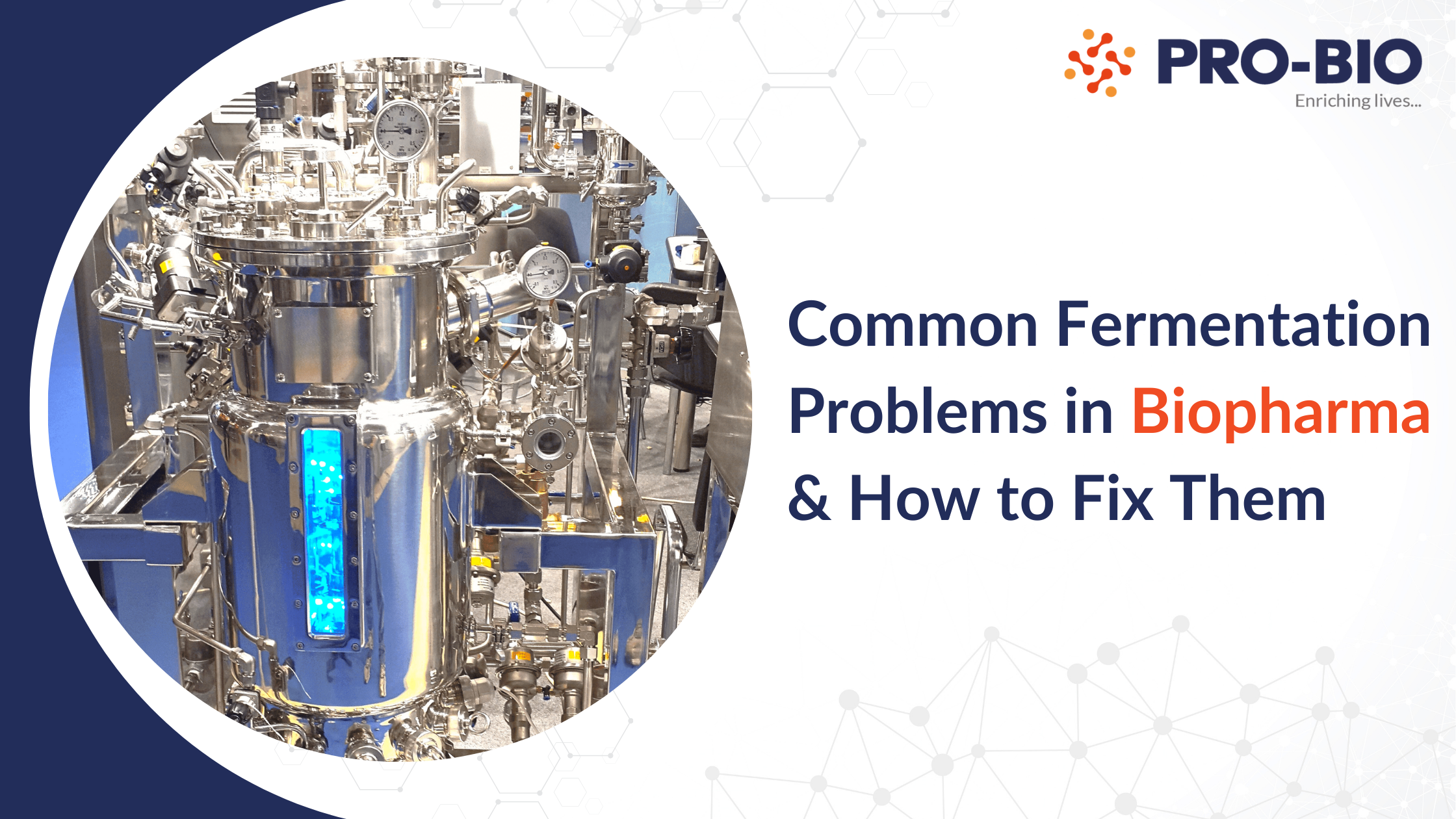
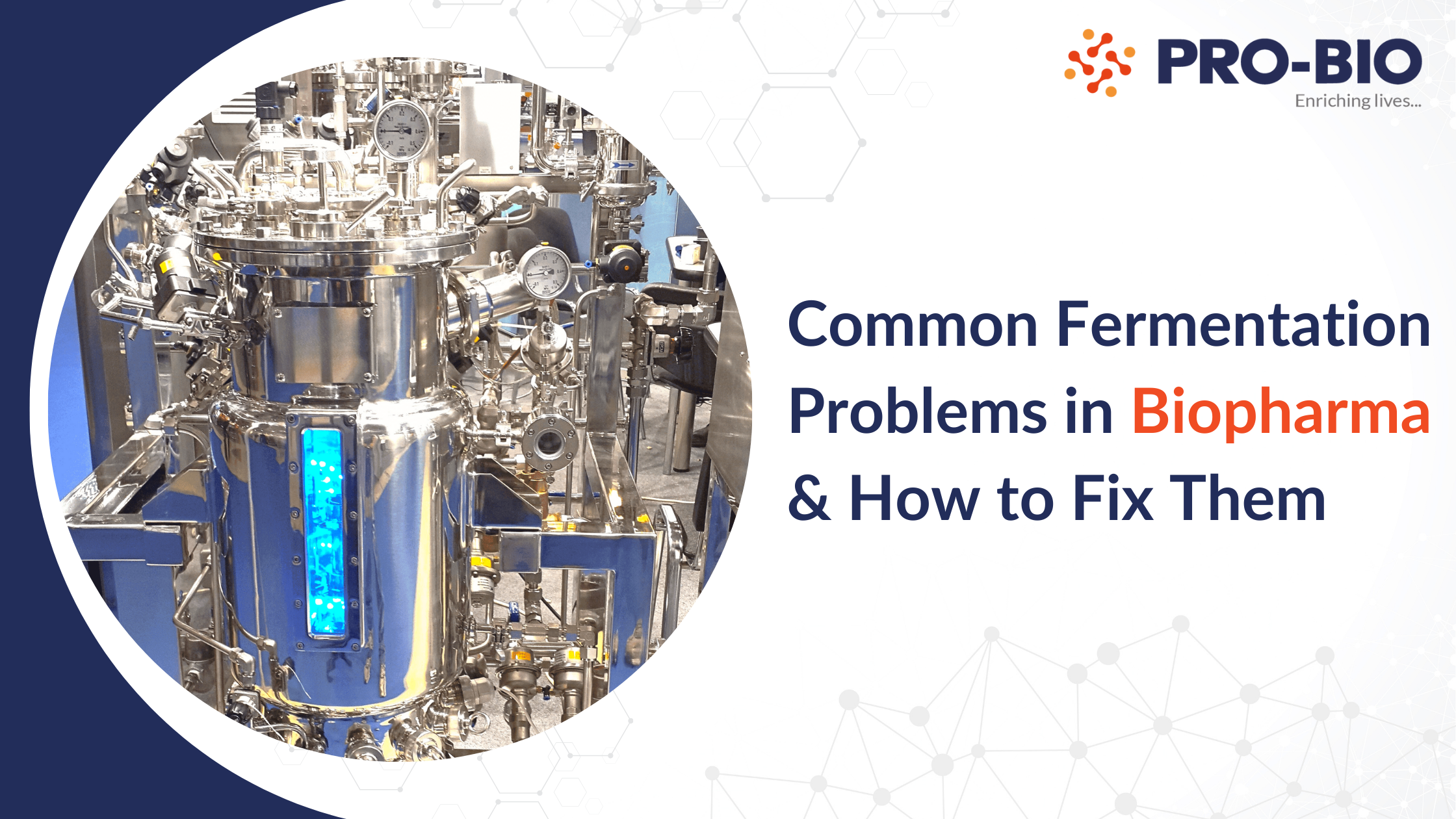
Fermentation is a core process in biopharmaceutical manufacturing, used for producing everything from recombinant proteins and enzymes to vaccines and cell therapies. However, it's also one of the most failure-prone stages of upstream processing.
From batch contamination to low oxygen transfer rates, small design flaws or process gaps in your fermentation tanks can lead to major production losses.
This guide explores the most common fermentation problems in biopharma, their root causes, and how modern GMP-compliant fermenters can solve them.
1. Contamination: The Silent Killer of Batches
Contamination is the #1 cause of fermentation failure in GMP facilities. It can stem from microbial ingress, faulty seals, or poor sterilization practices.
Impacts:
• Batch rejections• Equipment downtime
• Audit risks and potential regulatory flags
How to Fix It :
• Use CIP/SIP-capable fermenters with electro polished interiors• Eliminate dead legs with hygienic design
• Integrate magnetic mixers to avoid shaft leaks
• Install sterile air/gas filtration on all inlet lines
• Automate SIP cycles with validated temperature/pressure control
At Pro-Bio, our fermenters feature zero dead-leg design, fully automated SIP, and 316L electro polished stainless steel to mitigate contamination risks.
2. Foam Overflow and Sensor Damage
Foaming is common in microbial fermentation (especially E. coli and yeast), but uncontrolled foam can:
• Overflow into exhaust filters• Damage pH/DO sensors
• Interrupt oxygen transfer
How to Fix It:
• Add foam detection sensors with automated antifoam dosing• Use headspace spargers or mechanical foam breakers
• Ensure fermenter has adequate headspace design
• Optimize impeller type and RPM
Our fermenters support real-time foam control using sensor-based feedback and programmable dosing cycles.
3. Low Oxygen Transfer (OTR)
Oxygen transfer is critical for aerobic fermentation processes. Low kLa values result in poor cell growth and reduced yield.
How to Fix It :
• Use high-efficiency spargers and variable-speed agitation• Introduce pure oxygen sparging for high-density cultures
• Monitor DO with dual probes and adjust agitation based on feedback
• Maintain backpressure using precision valves
Our systems are designed for high kla delivery with modular gas panels and automated DO control for every fermenter size.
4. pH and Temperature Instability
Uncontrolled pH or temperature can:
• Denature proteins• Affect metabolite expression
• Lead to batch failure
How to Fix It:
• Use a temperature control unit (TCU) with tight feedback loop• Automate acid/base addition via pH probes
• Use insulated jackets to minimize heat loss
• Regularly calibrate temperature/pH sensors
Pro-Bio fermenters come pre-integrated with TCUs, SIP-capable pH probes, and automated control algorithms to ensure tight parameter regulation.
5. Poor Mixing and Shear Stress
Poor mixing causes dead zones, nutrient gradients, and potential shear damage to shear-sensitive cells like CHO or stem cells.
How to Fix It:
• Select proper impeller configuration (e.g., marine, Rushton, pitched blade)• Use bottom-mounted magnetic mixers for uniform low-shear blending
• Validate design with CFD or mixing studies
• Balance impeller RPM with gas sparging for optimal OTR/shear
We offer custom fermenter mixing systems optimized per product type—from microbial fermenters to mammalian cell bioreactors.
6. Manual Logging and Lack of Automation
Manual data entry can delay decision-making and risk non-compliance.
How to Fix It:
• Upgrade to PLC/SCADA-based fermentation systems• Implement remote monitoring and alarm handling
• Ensure compliance with 21 CFR Part 11 for electronic records
• Use batch trend logs for validation and troubleshooting
Our automation suite enables paperless batch records, real-time data capture, and cloud integration for QA teams.
Quick Checklist : Optimizing Your Fermentation Process
✅ CIP/SIP-ready fermenter with hygienic design✅ Real-time foam and DO control
✅ High-efficiency sparger and impeller systems
✅ Automated pH and temperature feedback
✅ Validated software with 21 CFR Part 11 compliance
✅ Magnetic mixing option for closed-loop systems
FAQs
Contamination, poor DO control, and manual operation are the top reasons for batch failure in GMP fermentation processes.
Use pure oxygen sparging, optimize mixing, maintain stable pH/temperature, and automate your control system.
ASME BPE surfaces, SIP/CIP design, traceability documentation, automated data logging, and compliance with 21 CFR Part 11.
Final Thoughts
Fermentation doesn't have to be unpredictable. With the right fermenter design, process controls, and automation, you can overcome the most common pain points in biopharma fermentation.
At Pro-Bio, we build custom-engineered fermenters that help:
• Improve yield• Reduce contamination
• Automate batch control
• Meet regulatory standards
Whether you're working with microbial fermenters, mammalian cell culture, or pilot to production-scale tanks, we have a solution.
Ready to Fix Fermentation Issues?
📞 Talk to Our Experts📩 Request a Quote
🔎 Explore our Fermenter Systems