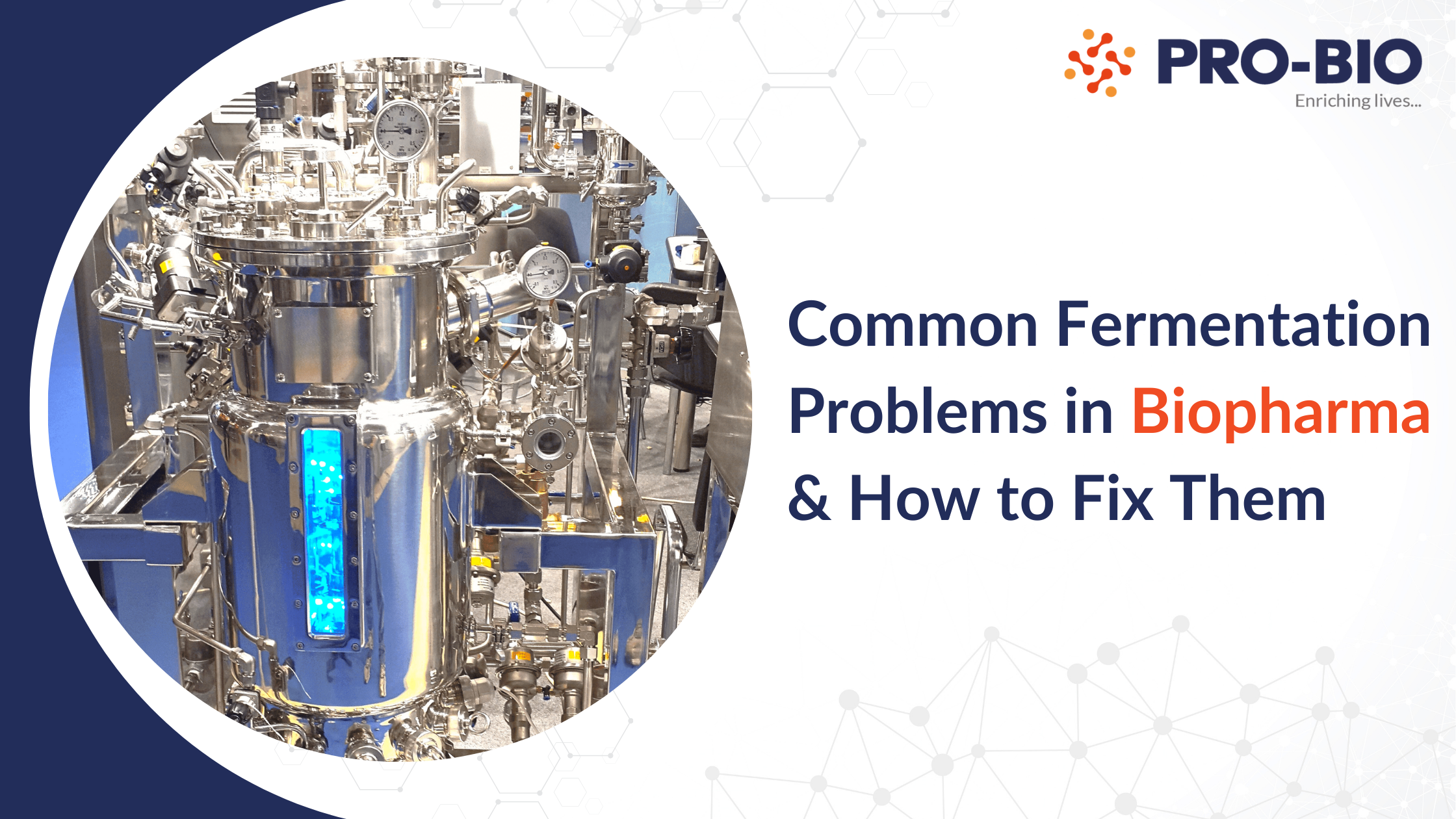

Tangential Flow Filtration (TFF) is a cornerstone of downstream processing in biopharmaceutical manufacturing used to concentrate, dia filter, and purify proteins, antibodies, and other biologics.
But if you’re experiencing low product recovery, your TFF system could be costing you millions over time.
This guide outlines the key causes of low product recovery in TFF systems, and what you can do to troubleshoot, redesign, or optimize your setup for higher yield and consistency.
What Is Product Recovery in TFF?
Product recovery is the percentage of your target molecule that you retrieve after a TFF run, compared to what you started with.
If you’re processing 10 litters of mAb solution and recovering only 85%, you're losing 1.5 litters of high-value product potentially tens of thousands of dollars per batch.
1. High Hold-Up Volume in the Filtration Skid
A common but overlooked cause of yield loss is hold-up volume product trapped in:
• Tubing• Pump heads
• Connectors
• Filters
How to Fix It:
• Use shorter tubing and smaller internal diameters• Choose low-hold-up valves and pumps (e.g., diaphragm types)
• Add drain ports at system low points
• Consider single-use flow paths for minimal retention
Our custom-engineered TFF filtration skids are designed with ultra-low hold-up volume to maximize product yield.
2. Incorrect Membrane Selection
The membrane material and pore size (MWCO) must match your molecule’s size. Using the wrong membrane can cause:
• Product to pass into permeate (lost)• Product to foul and clog membranes
How to Fix It:
• For mAbs, use 10–30 kDa MWCO membranes• For enzymes/proteins, match MWCO to ~1/3 of the molecule’s size
• Choose hydrophilic membranes to reduce adsorption
• Run small-scale membrane trials before scale-up
We assist in membrane selection with every TFF skid to ensure performance before you go to production.
3. Fouling and Adsorption to the Membrane
Proteins can stick to membrane surfaces (adsorption) or clog pores (fouling), especially in:
• Poorly buffered feeds• Highly concentrated solutions
How to Fix It:
• Optimize feed buffers to stabilize proteins• Use low-protein-binding membranes (e.g., PES)
• Clean between runs with validated CIP cycles
• Monitor TMP (transmembrane pressure) for fouling spikes
Our systems feature real-time TMP and conductivity monitoring for proactive fouling management.
4. Suboptimal Operating Parameters
TFF runs can underperform when process variables aren't dialled in, such as:
• Crossflow rate• TMP (Transmembrane Pressure)
• Retentate flow rate
• Diafiltration speed/volume
How to Fix It:
• Balance crossflow vs. shear sensitivity• Maintain TMP in the 1–2 bar range
• Use conductivity steps to validate diafiltration
• Automate parameters with PID control
We offer fully automated UF/DF TFF filtration systems for consistent, high-yield performance.
5. Incomplete Product Recovery After the Run
Even after a good TFF run, residual product can stay in:
• Membrane channels• Retentate lines
How to Fix It:
• Run flush cycles with buffer or WFI• Use reverse flow to dislodge trapped product
• Displace with air or nitrogen purge
• Automate as part of your batch control recipe
Our systems include post-run recovery logic, consistently achieving >99% product recovery.
6. Dead Legs and Incomplete Drainability
Poor mechanical design causes “dead zones” — areas with no flow where product collects or contaminants grow.
How to Fix It:
• Design to ASME BPE standards• Eliminate T-junctions and oversized pipes
• Ensure all piping is gravity-drainable
• Validate drainability during FAT/SAT
We use 3D flow simulation and drain mapping to engineer fully drainable TFF skids.
Quick Recap: TFF Yield Loss Issues & Fixes
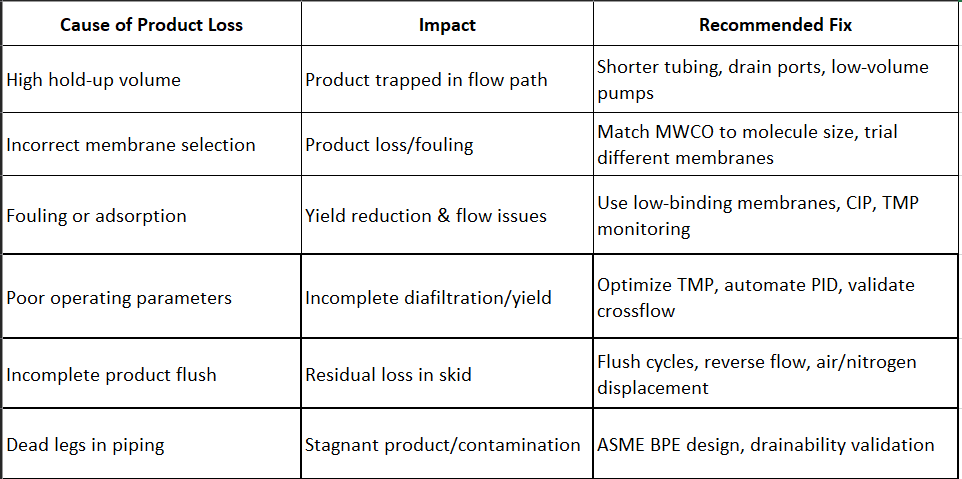
FAQs
Typically 95–99% is achievable with optimized skid design and membrane selection.
Use low-binding membranes, optimize TMP, reduce hold-up volume, and perform product flush steps.
High hold-up volume, membrane adsorption, poor diafiltration settings, and system dead legs.
Final Thoughts
Low product recovery in tangential flow filtration isn’t just a technical issue — it’s a financial one.
Whether you're purifying monoclonal antibodies, enzymes, or plasma-derived products, improving recovery even by 2–3% can significantly impact your bottom line.
At Pro-Bio, we design lab and production-scale TFF systems engineered to deliver:
• High recovery yields
• Full process automation
• GMP-compliant performance
Ready to Improve Product Recovery in Your TFF System?
📞 Talk to Our Experts📩 Request a Quote
🔎 Explore Our TFF Systems