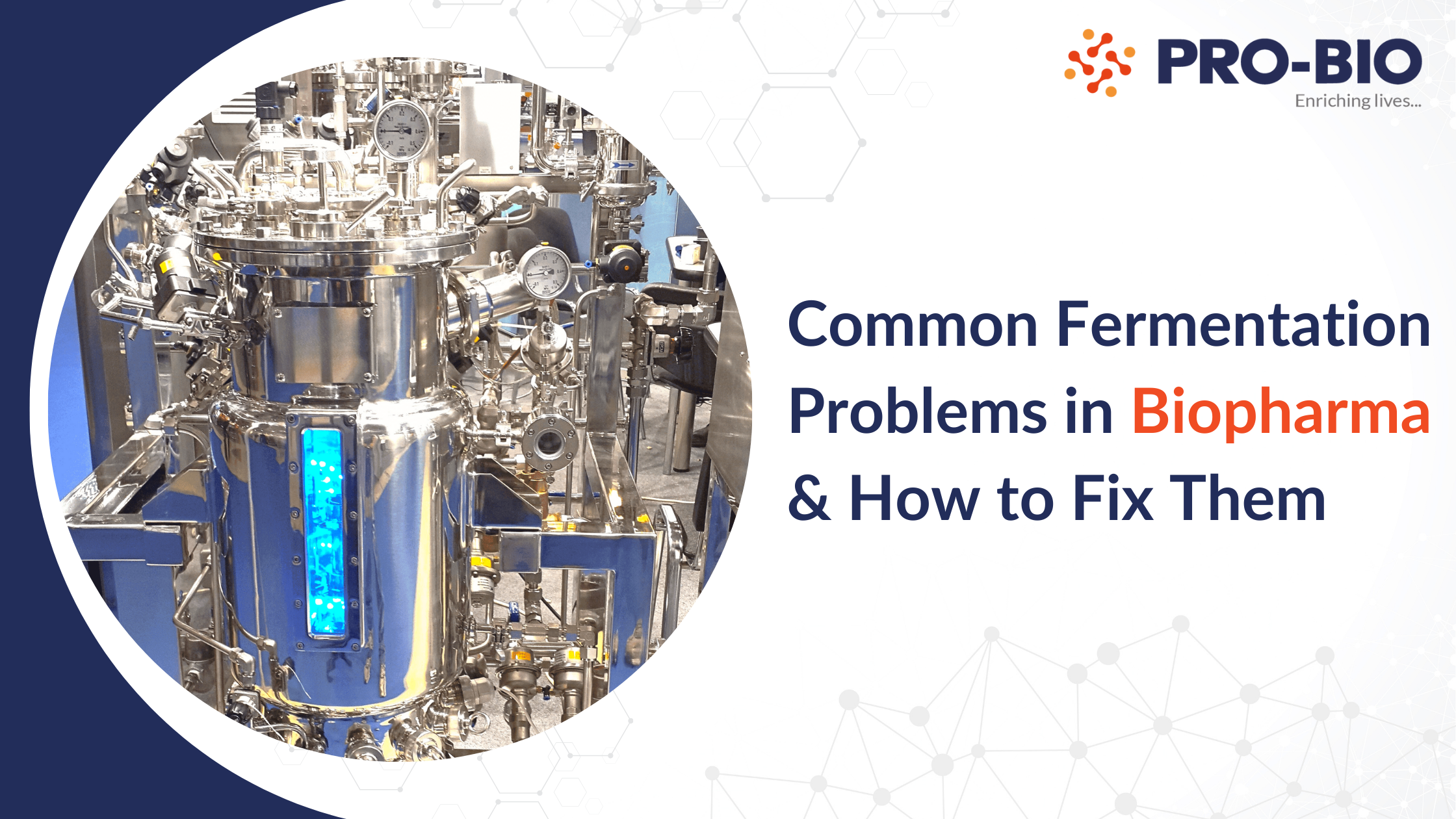
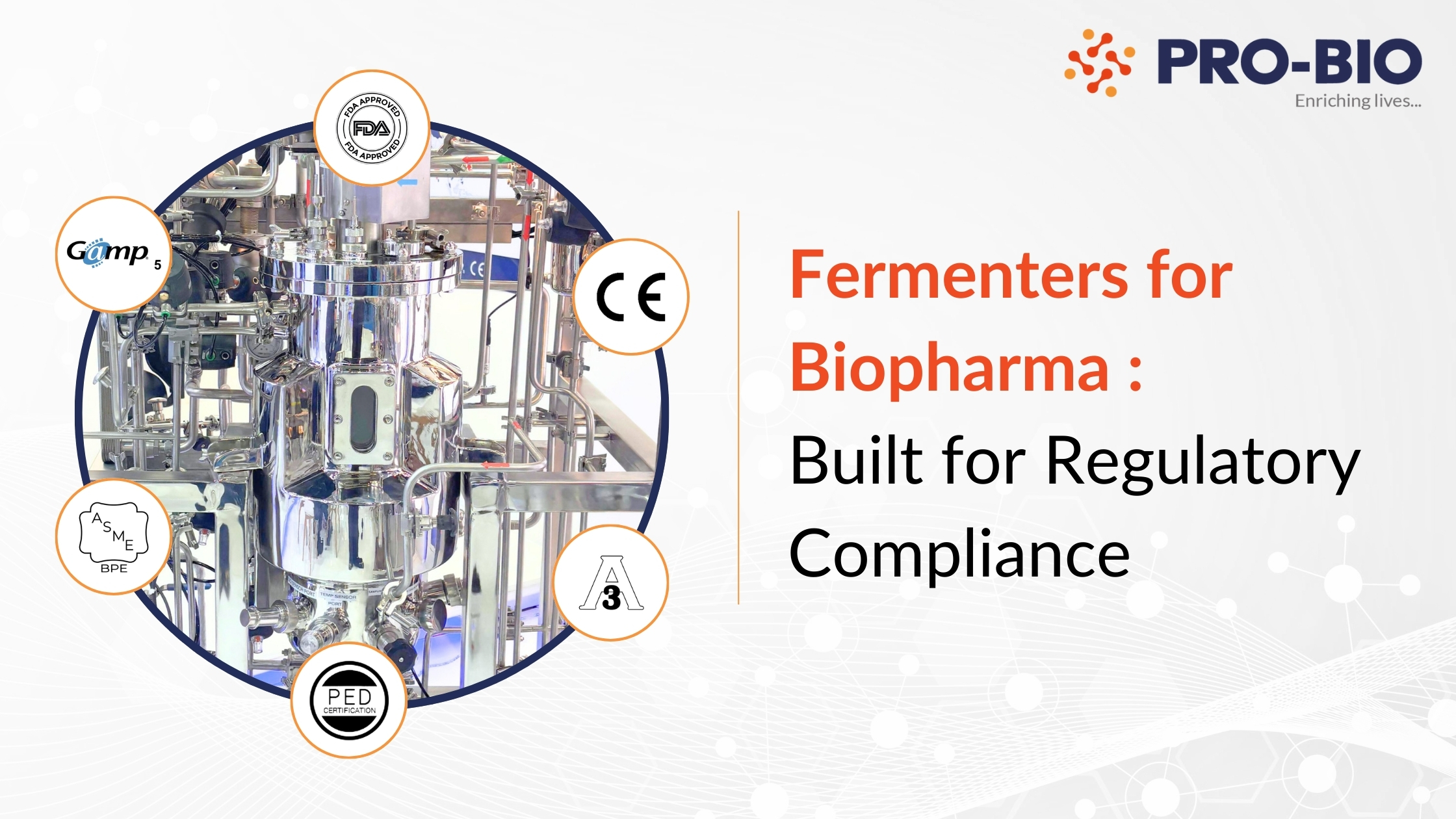
In biopharmaceutical manufacturing, compliance with stringent regulatory frameworks is a cornerstone of operational excellence.
Global regulatory bodies such as the FDA, UL, and ASME BPE set rigorous standards for equipment design, validation, and operation. These requirements ensure product safety, traceability, and facility biosafety especially in processes involving live microbial fermentation or cell culture.
This blog explores how modern biopharma fermenters are engineered to meet these critical regulatory demands and how the right system can help your facility stay audit-ready, batch after batch.
1. Designing for FDA Compliance
Fermenters must support aseptic processing and full traceability.
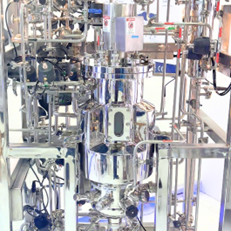
Key FDA-compliant features:
• Zero dead-leg sampling valves• Flush-bottom valves for full drainability
• 21 CFR Part 11-compliant data logging
• Contamination-resistant surface finishes and welding
Integrated automated controls help simplify reporting and audit readiness.
2. ASME BPE: The Gold Standard in Bioprocess Equipment
ASME BPE governs hygienic equipment standards for bioprocessing:
• Electropolished SS316L interior (Ra < 0.38 µm)• High-purity elastomers
• Orbital welds and hygienic flanges
• Designed for cleanability and cross-product use
Fermenters built to this standard ensure repeatable sterility and minimal validation burden.
3. UL Certification: Electrical Safety You Can Trust
UL-rated systems reduce fire and electrical risks:
• Certified control panels and agitators• Tested wiring systems
• Regulatory recognition in global markets
• Suitable for classified environments
Every Pro-Bio fermenter ships with UL-compliant schematics and safety documentation.
4. EX Standards: For Hazardous or Explosive Environments
For processes involving volatile materials, EX compliance is non-negotiable:
• Explosion-proof motors• Intrinsically safe sensors
• ATEX or IECEx-rated instrumentation
• Integrated gas leak and spark suppression logic
These systems support fermentation under BSL-2/BSL-3 biosafety protocols.
Compliance Checklist: What to Expect from a Regulatory-Ready Fermenter
✅ Electropolished SS316L with ASME BPE finishes✅ UL/EX-certified electrical components
✅ 21 CFR Part 11-compliant PLC/SCADA systems
✅ CIP/SIP integration
✅ IQ, OQ, FAT/SAT documentation
✅ Traceable MOC (material of construction) for all wetted parts
✅ Hygienic, drainable design for easy validation
5. Traceability and Validation: Built In
Traceability isn’t optional — it’s a core requirement.
All our fermenters include:
• MTCs, weld logs, passivation certificates
• 3D layout drawings and P&IDs
• Integrated SCADA batch reports
These elements drastically reduce QA effort and audit prep time.
6. Supporting Sustainability Goals
Today’s fermenters are also expected to be eco-conscious:
• Advanced insulation to reduce heat loss• Low-waste cleaning cycles
• Recyclable material choices
• Support for clean utility loops (WFI, pure steam)
Our systems align with global environmental compliance frameworks.
FAQs
FDA (21 CFR Part 11), ASME BPE, UL, and EX — based on process and region.
Yes - if designed with ASME BPE standards and full CIP/SIP support.
Strongly recommended - especially for motorized systems and automated lines.
Final Thoughts
Regulatory compliance is one of the biggest challenges in biopharma facility design and the fermenter is at the centre of that ecosystem.
At Pro-Bio, we manufacture GMP-grade fermenters that meet the highest global standards:
✅ FDA-compliant✅ ASME BPE certified
✅ UL/EX safe
✅ Built for easy qualification and validation
Ready to Simplify Compliance with the Right Fermenter?
📞 Talk to Our Experts📩 Request a Quote
🔎 Explore our Bio-Fermenter Systems